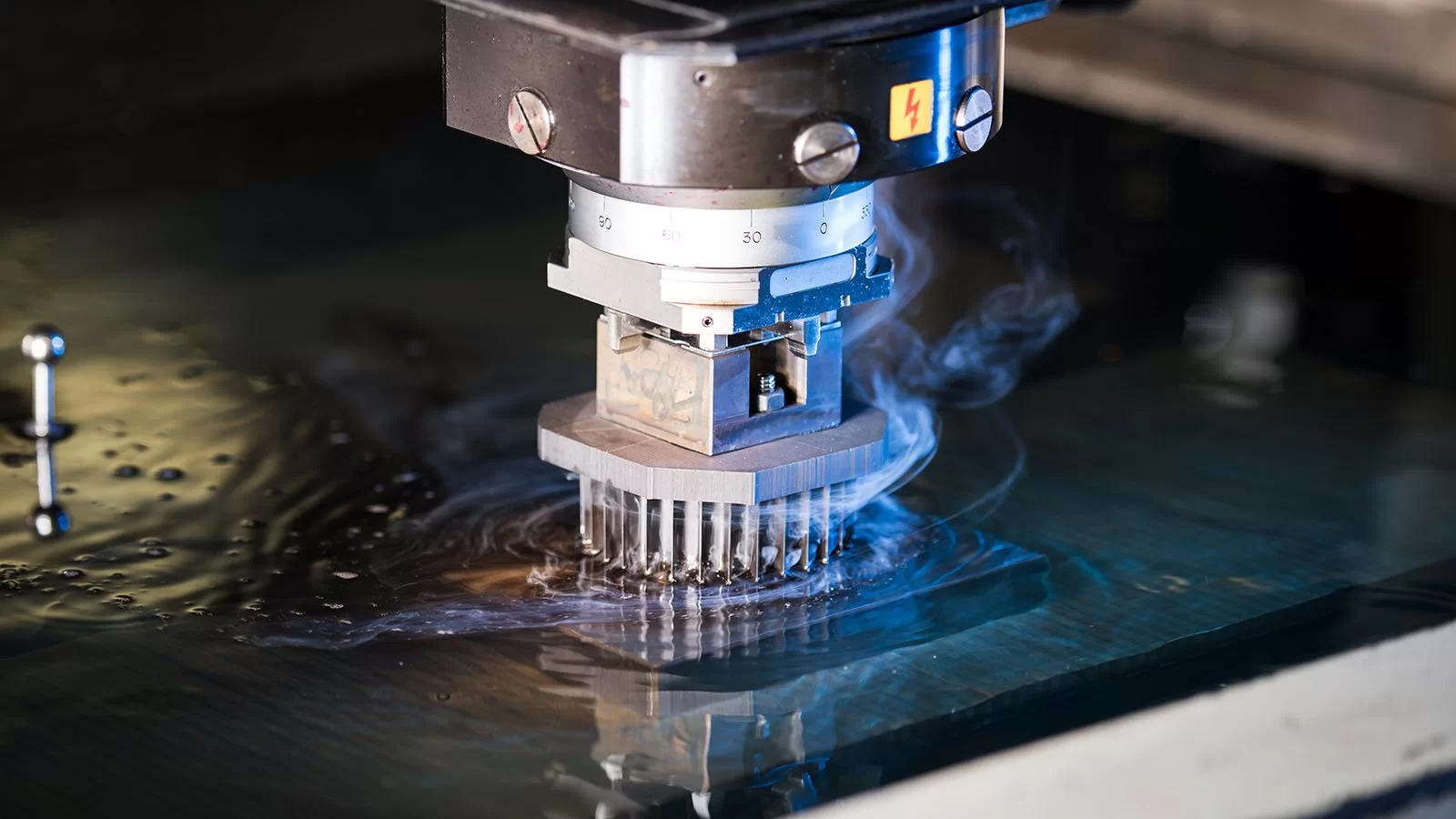
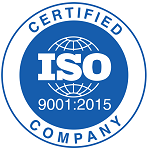
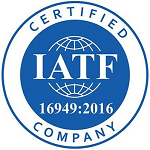

Injection Moulding
Our Mould Making Capability
Prototype Mould
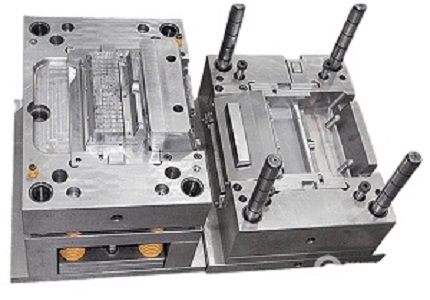
- Short lead-time: down to 3 days
- Limited lifespan depends on the purpose
- Normally based on aluminum
- Lower cost
Production Mould
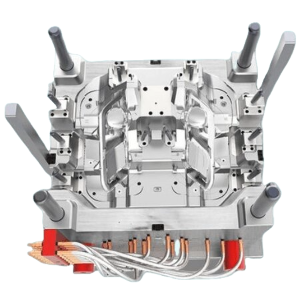
- Long lifespan: up to 1M units
- Automated production for cost-efficiency at higher volumes
- Hardened steel for longer life with a scalable unit price
Single Cavity Mould
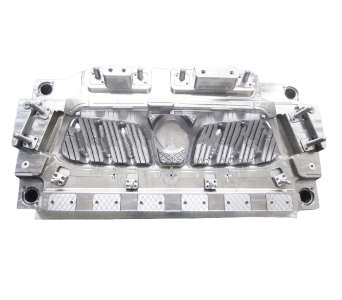
- Ideal for high-precise and high-quality plastic parts
- Ideal for big dimension parts
- More flexibility for design cha.nges and customization
Multi-cavity Mould
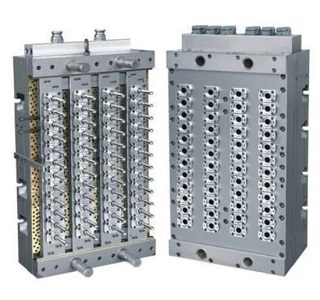
- Significantly increasing production efficiency
- Ideal cost-effective choice for high-volume production
- Ensure good consistency and uniformity in dimensions and quality
Stack Mould
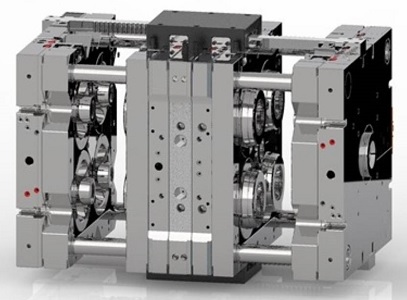
- Cost-effective with reducing the injection moulding cycles
- Possible to achieve multi-colored or multi-material parts in one process
- Suitable for large flat products with small shapes and multi-chamber
Over&Insert-moulding Mould
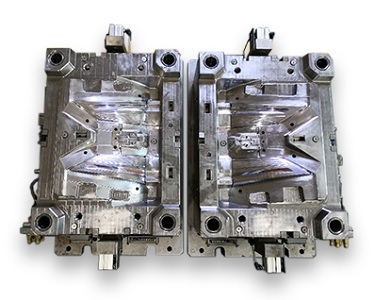
- Reduced manufacturing costs with eliminating assembly steps
- Enhanced product functionality, comfortableness and aesthetics
- Increased product durability with additional layer of protection
- Our tolerance options are in accordance with ISO 20457/DIN 16742
- A typical tolerance is ± 0.1 mm while a very tight tolerance is ± 0.025 mm
- Tolerance depends on the material, geometry, shrinkage and son on
Our Mould Class & Property
Mould Class | Production Cycles | Mould Material | Hardness (BHN) | Description |
---|---|---|---|---|
101 | >1 million | Heat-treated stainless steel | 280 | The highest quality materials and highest price, for the products with extremely high volume production |
102 | <1 million | Heat-treated tool steel | 280 | Fairly high price with materials of high quality, good for parts with abrasive materials and tight tolerances |
103 | <50,000 | P20 Steel | 165 | Common price range, widely used for low to medium volume production parts |
104 | <10,000 | Mild steel, aluminium, alloys | <165 | Low to mid price range, good for limited-production parts especially with non-abrasive materials |
105 | <500 | Soft aluminum, epoxy, cast materials | <165 | Low price, mostly used for prototype with a limited volume production |
Injection Moulding
Our Mould Surface Finishes
SPI Finish
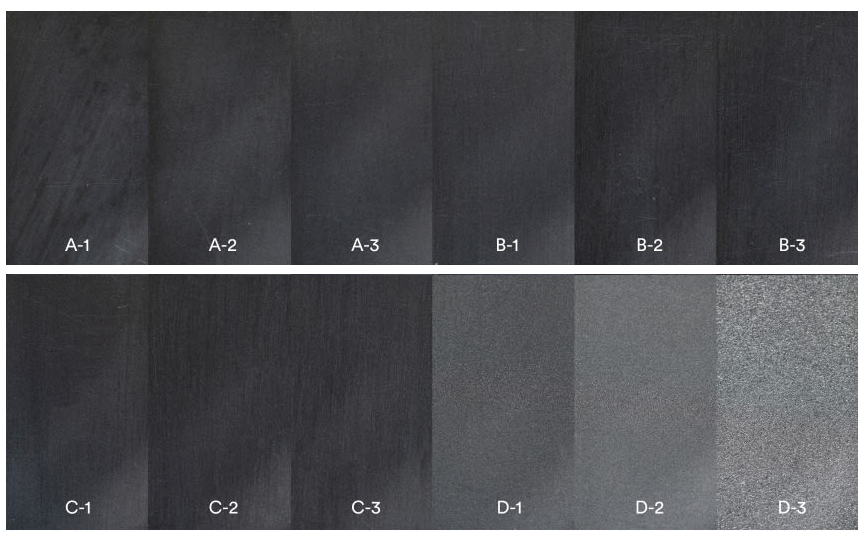
Standard | Finishing Method | Surface Roughness Ra (μm) | Finish Look |
---|---|---|---|
A1 | Grade #3, 6000 Grit Diamond Buff | 0.012 to 0.025 | Super High Glossy |
A2 | Grade #6, 3000 Grit Diamond Buff | 0.025 to 0.05 | High Glossy |
A3 | Grade #15, 1200 Grit Diamond Buff | 0.05 to 0.10 | Normal Glossy |
B1 | 600 Grit Paper | 0.05 to 0.10 | Fine Semi-glossy |
B2 | 400 Grit Paper | 0.10 to 0.15 | Medium Semi-glossy |
B3 | 320 Grit Paper | 0.28 to 0.32 | Normal Semi-glossy |
C1 | 600 Grit Stone | 0.35 to 0.40 | Fine Matte |
C2 | 400 Grit Stone | 0.45 to 0.55 | Medium Matte |
C3 | 320 Grit Stone | 0.63 to 0.70 | Normal Matte |
D1 | Dry Blast Glass Bead #11 | 0.80 to 1.00 | Satin Textured |
D2 | Dry Blast #240 Oxide | 1.00 to 2.80 | Dull Textured |
D3 | Dry Blast #24 Oxide | 3.20 to 18.0 | Rough Textured |
- We offer all types of SPI Finish
- SPI Finish is mainly used for mould polish, focusing on “SMOOTH”
- SPI Finish refers to the American surface finish standard set by SPI (Society of the Plastics Industry)
Surface Finish
VDI 3400 Texture
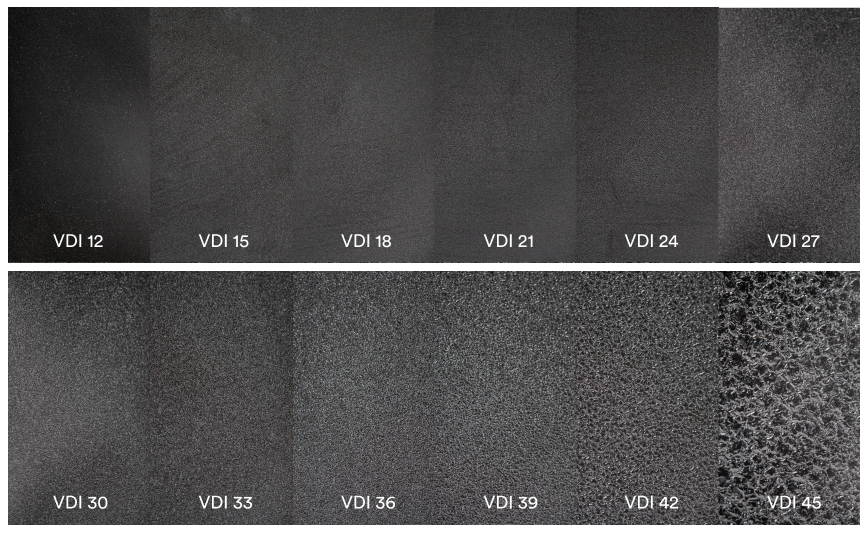
Standard | Finishing Method | Surface Roughness Ra (μm) | Finish Look |
---|---|---|---|
12 | 600 Stone | 0.40 | Low polish |
15 | 400 Stone | 0.56 | Low polish |
18 | Dry Blast Glass Bead | 0.80 | Satin finish |
21 | Dry Blast # 240 Oxide | 1.12 | Dull finish |
24 | Dry Blast # 240 Oxide | 1.60 | Dull finish |
27 | Dry Blast # 240 Oxide | 2.24 | Dull finish |
30 | Dry Blast # 24 Oxide | 3.15 | Dull finish |
33 | Dry Blast # 24 Oxide | 4.50 | Dull finish |
36 | Dry Blast # 24 Oxide | 6.30 | Dull finish |
39 | Dry Blast # 24 Oxide | 9.00 | Dull finish |
42 | Dry Blast # 24 Oxide | 12.50 | Dull finish |
45 | Dry Blast # 24 Oxide | 18.00 | Dull finish |
- We offer all types of VDI 3400 Texture
- VDI 3400 Texture is a reference for surface roughness, focusing on “ROUGH”
- VDI 3400 Texture refers to the texture standard set by Verein Deutscher Ingenieure (VDI)
Injection Moulding
Our Secondary Processes
Spray Painting
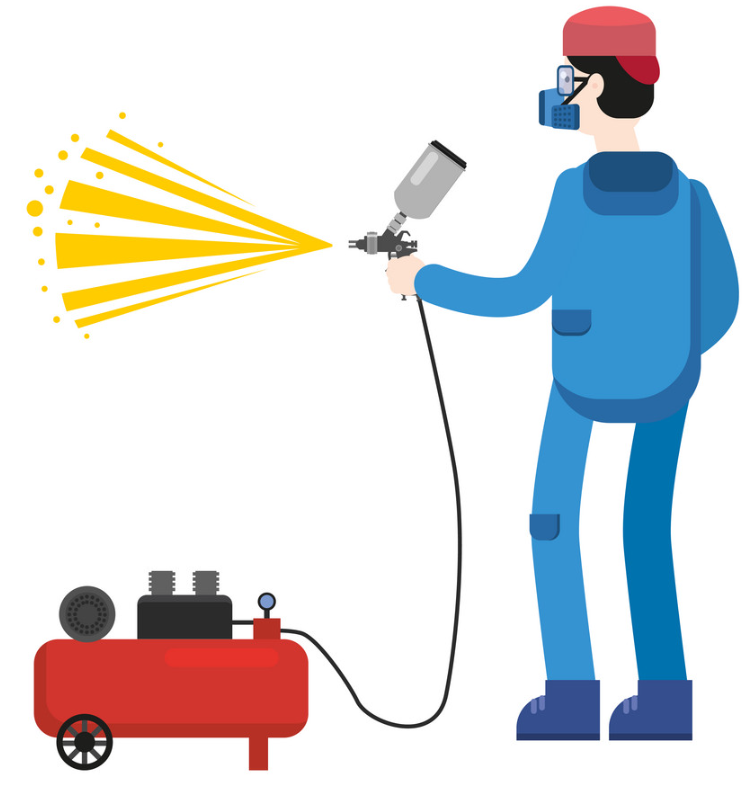
The simplest and most cost-effective painting process used to add color or character onto plastic parts. Some paints are two-part and self-curing when the others require UV curing.
Powder Coating
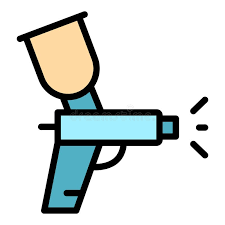
A powdered plastic is sprayed onto the parts and then a UV curing is used to adhere it to the surface. Powder coating can provide a tough, long-lasting finish on plastic injection moulded parts.
Screen Printing
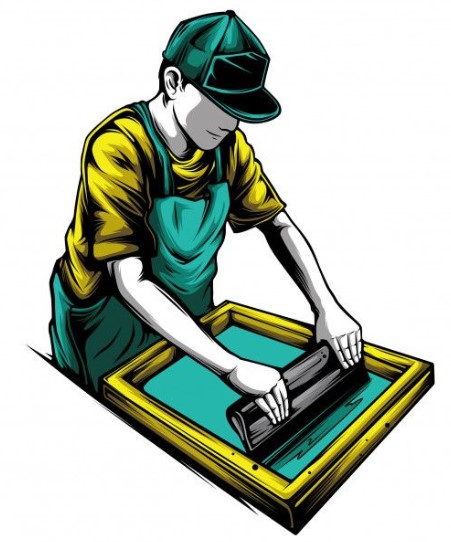
A type of stencil is created on fine mesh, with several layers of ink pushed through this stencil layout onto the surface of the print material. A cost-effective approach for multi-color appearance.
Laser Engraving
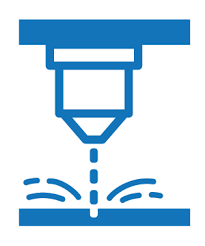
Mostly used for particularly precise and complex patterns. It’s an automated process working with a wide variety of materials of varying degrees of thicknesses.
Pad Printing
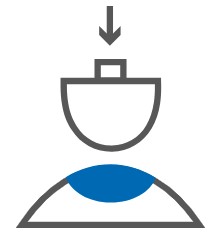
Ideal for personalized or customized products, using multiple colors to print images on highly chemical-resistant surfaces.
Electroplating
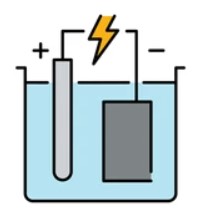
Provides the ability for a non-conductive plastic surface to conduct electricity, protects a plastic part from corrosion, enhances the appearance.
- We also offer more processes such as welding, machining, assembly, etc
- Customized new processes are also possible to be developed
Injection Moulding
Product Gallery
Injection Moulding
Industry Applications
Automotive

Industrial Machinery
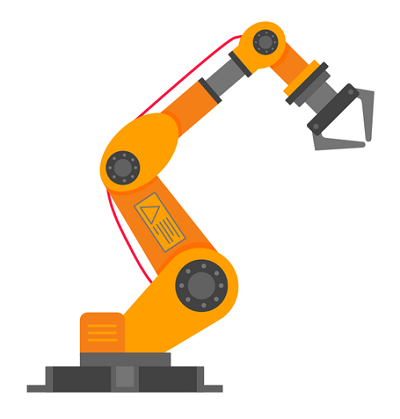
Renewable Energy

Medical & Healthcare
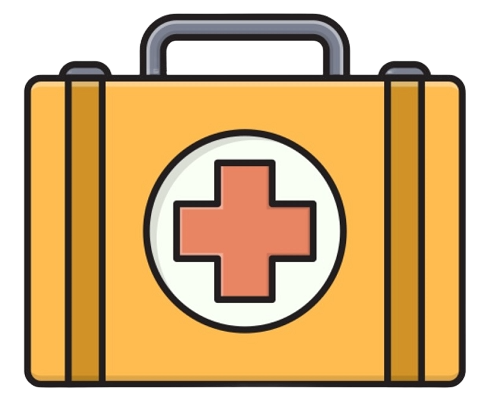
Consumer Products & Electronics
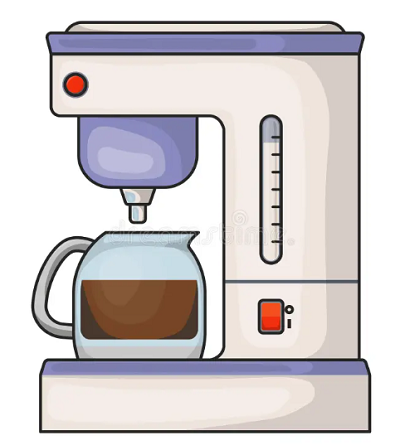
Injection Moulding
Material Selection
Type of Resin | Benefits | Applications | Considerations |
---|---|---|---|
PC (Polycarbonate) | Strong, extremely impact resistant, low shrink, good dimensional stability and heat resistance, accepts high cosmetic finishes well. | Lenses, indoor and outdoor lighting, cell phone housings, electrical components, medical devices, bulletproof glass. | Possible sensitivities in thick sections of parts could cause voids, bubbles, and sink. Poor chemical resistance. An ABS/PC blend is a good alternative for opaque parts with these issues Acrylic is another option for parts with thick geometries. |
PMMA or Acrylic (Polymethyl Methacrylate) | Good optical properties, high gloss, scratch resistant. Low shrink, Less sink in geometries with thin and thick sections. | Light pipes, lenses, light shades, optical fibers, signs. | Can be brittle. PC is a good alternative. Draft always required, sometimes twice as much as other materials. Poor chemical resistance. |
ABS (Acrylonitrile butadiene styrene) | Tough, impact- and chemical-resistant, low shrink, high dimensional stability, inexpensive. | Cosmetic parts, handheld devices, housings, and moldings for electrical tools, remote controls, computers, telephone components | Show knit lines and can have sink and voids in thick areas. You might be able to reduce sink by switching to an ABS/PC-blend. |
PC/ABS | Strength, heat and low-temperature resistance, improved processing, | Automotive, electronic, telecommunications | Improved thick molding and mechanical properties compared to just ABS or PC. Lower cost than PC. |
PP (Polypropylene) | Inexpensive, higher impact resistance in some grades, PP homopolymer can be brittle in cold. Wear resistant, flexible with high elongation. Resistant to acids and bases. Density less than water (floats) | Integral hinges or living hinges, fans, snap-over lids (e.g., shampoo bottle tops), medical pipette tubing | Thick sections in part geometry can void or show sink marks. Shrink and warp possible. If the part has living hinges that require higher stiffness, K-Resin is a good alternative. |
POM or Acetal (Polyoxymethylene) | Tough, stiff, hard, and strong. Good lubricity and resistance to hydrocarbons and organic solvents. Good elasticity, slippery. Low creep. Great fatigue properties. | Gears, pumps and pump impellers, conveyor links, soap dispensers, fan and blower blades, automotive switches, electrical switch components, buttons, and knobs. | Due to shrink, you need uniform wall thickness. Painting, coating, and achieving high-cosmetic finish difficult. |
HDPE (High-density polyethylene) | Tough, impact- and chemical-resistant, high shrink, low dimensional stability, inexpensive, density less than water (floats) | Lawn furniture, totes, containers, toys, gas cans, etc. | High shrink, low surface energy. |
PS (Polystyrene) | High optic clarity, good electric insulator. | Plastic utensils, containers, optics, toys. | brittle, poor UV resistance, very susceptible to hydrocarbon solvents. |
PEEK (Polyether Ether Ketone) | High-temperature, high-performance, flame retardant; excellent strength and dimensional stability, good chemical resistance | Bearings, piston parts and pumps; cable insulation; compatible with ultra-high vacuum applications. | High-performance material, very expensive. Ultem (outlined below) is a slightly less-costly option, and PPSU is worth considering if price is a concern. |
PEI or Ultem (Polyetherimide) | High-temperature, high-performance, flame retardant, excellent strength and dimensional stability, good chemical resistance. | Medical and chemical instrumentation; tableware and catering; HVAC and fluid handling; electrical and lighting. | Very expensive, though not as costly as PEEK. Look at PPSU as a possible alternative. |
PPSU (Polyphenylsulfone) | High-temperature tolerance, dimensionally stable, high toughness. Resistance to radiation sterilization, as well as alkalis and weak acids | Medical instrument components, sterilization trays, automotive fuses, interior aircraft parts, hot water fittings, sockets, and connectors. | Thick sections could result in voids, bubbles or sink. Organic solvents and hydrocarbons can also attack PPSU. Colorant cannot be added to Protolabs-supplied PPSU resins |
PA (Polyamide or commonly called nylon) | Wide variety. High strength and temperature tolerance when reinforced. Chemically resistant except to strong bases or acids | Thin-walled features, combs, spools, gears and bearings, screws, structural parts (with glass), pump parts, under-hood components, cameras. | Some nylons can be susceptible to warp due to non-linear shrink. Absorbs moisture, causing issues. |
PPA (Semi-aromatic Polyamides) | less susceptible to moisture than aliphatic polyamides | automtive housings, modules, valves, sports equipment | susceptible to warp |
PBT (Polybutylene Terephthalate) | Good electrical properties for power components and works well for automotive applications. Moderate to high strength depending on glass fill. Unfilled grades are tough and flexible. Good resistance to fuels, oils, fats, and many solvents. Doesn’t absorb flavors. Low creep. | Slide bearings, gears and cams; coffee makers and toasters; hair dryer nozzles; vacuum cleaners; handles and knobs for electrical cookers. | Glass-filled PBT resins are prone to warp, and have poor resistance to acids, bases, and hydrocarbons. Thin parts hard to fill with PBT. Nylons are good alternatives. |
PET (Polyethylene Terephtalate) | similar to PBT, but stiffer and higher melting point | similar to PBT | similar to PBT |
LCP | very easy flowing, good chemical resistance, high upper use temp, good electrical properties, low thermal expansion | connectors, plugs, PCBs, sports equipment | anisotropic properties and shrinkage, expensive |
PPO | good electrical insulator, hot water / steam resistance | sensor housings, pumps, connectors | susceptible to stress cracking |
PPS | very good chemical resistance, high upper use temp, great electrical properties | electric components, automotive intakes / pumps / valves / sensor encapsulation | desirable properties, such as chemical resistance rely heavily on proper crystallization during molding |